Diese Website verwendet Cookies, damit wir dir die bestmögliche Benutzererfahrung bieten können. Cookie-Informationen werden in deinem Browser gespeichert und führen Funktionen aus, wie das Wiedererkennen von dir, wenn du auf unsere Website zurückkehrst, und hilft unserem Team zu verstehen, welche Abschnitte der Website für dich am interessantesten und nützlichsten sind.
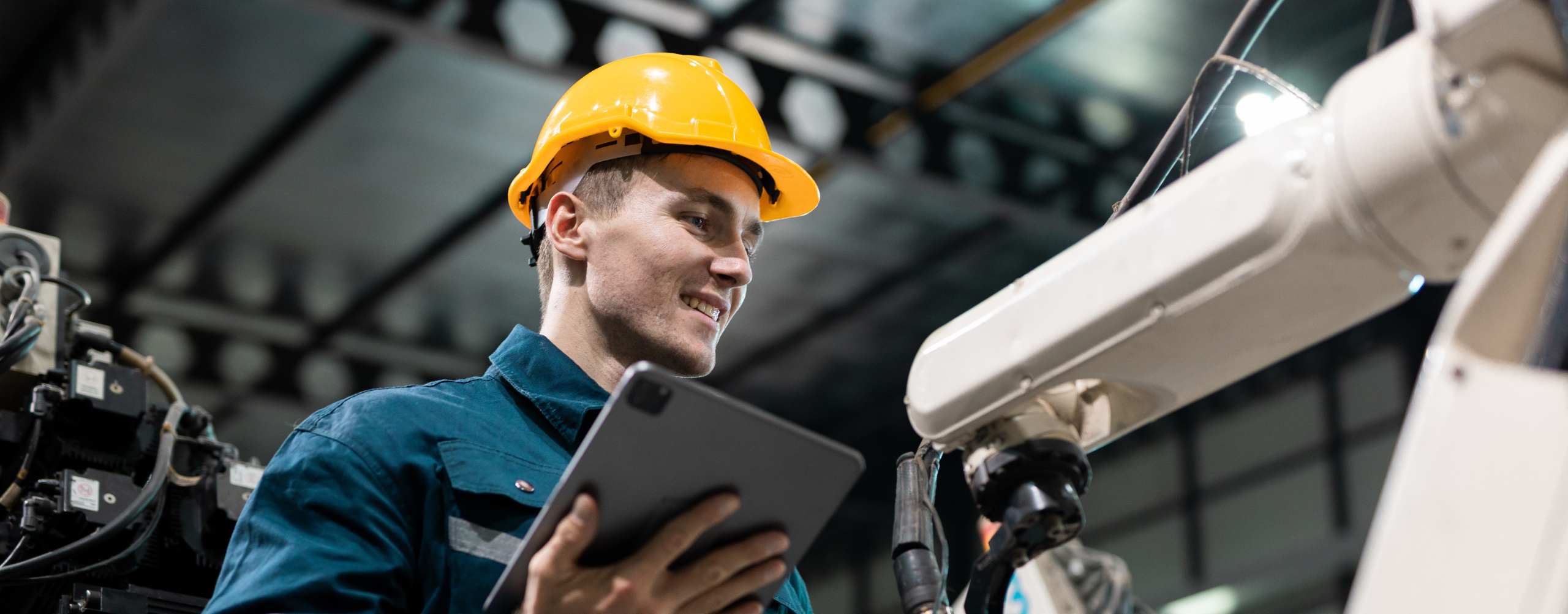
Kunde
Ein führender Hersteller von Metallkomponenten in Nordamerika. Das Unternehmen setzte zwei Maschinentypen ein: eine moderne, aber energieintensive Maschine und eine ältere, wartungsarme Maschine, die jedoch manuell bedient werden musste.
Herausforderung
In einer der Fabriken in Toronto wurden täglich hunderte Metallteile geschnitten – von einfachen Formen bis hin zu komplexen Geometrien. Die Produktion basierte auf zwei Maschinen:
- Einer modernen, vollautomatisierten, aber teuren Maschine
- Einer älteren, kostengünstigeren Maschine, die jedoch manuell für jedes neue Projekt eingerichtet werden musste
Aus Kostensicht war der Einsatz der älteren Maschine deutlich wirtschaftlicher (die Produktionskosten pro Teil lagen bei der Hälfte). Ihr Betrieb brachte jedoch zahlreiche Herausforderungen mit sich:
- Stundenlange Analyse der DXF-Dateien und manuelle Einstellung der Parameter
- Hohes Fehlerrisiko, was zu Material- und Zeitverlusten führte
- Überlastung der teureren Maschine und unzureichende Ausnutzung der günstigeren
- Zu hoher Energieverbrauch und vermeidbare Betriebskosten
Vier Jahre lang versuchte das Unternehmen vergeblich, den Prozess der Auftragsverteilung auf die Maschinen zu optimieren. Um die Kosten tatsächlich zu senken, wurde eine Lösung benötigt, die diesen Prozess automatisiert – damit die kostengünstigere Maschine mit der gleichen Präzision und Geschwindigkeit arbeiten kann wie das moderne Modell.
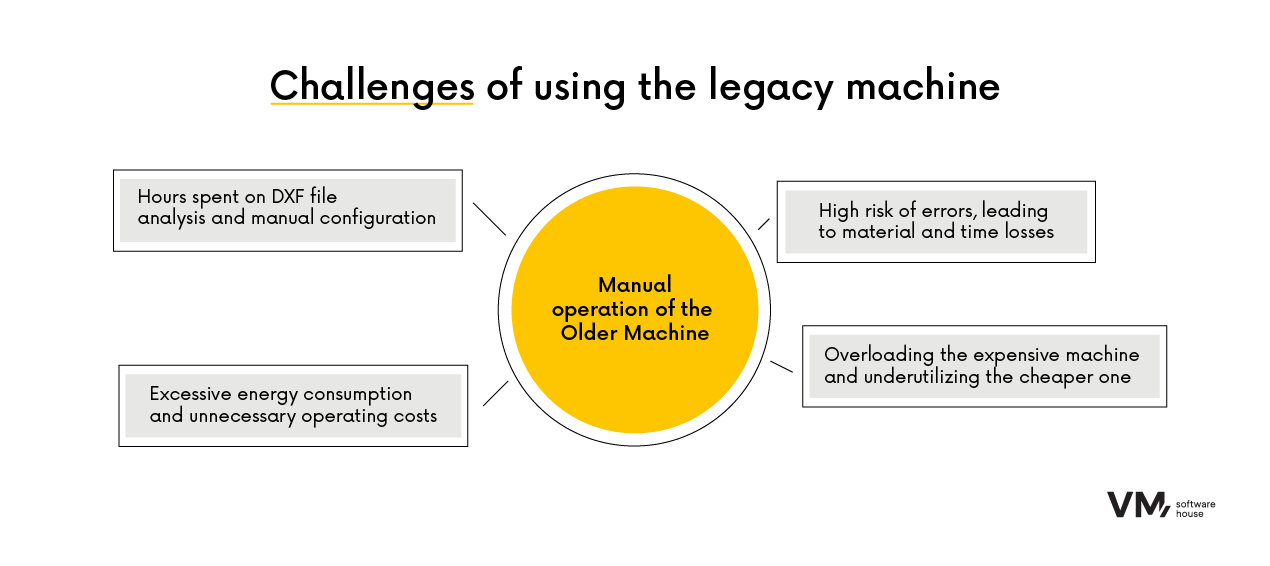
Lösungsansatz
Wir entwickelten ein Machine-Learning-basiertes System zur Formerkennung, kombiniert mit einem regelbasierten Algorithmus zur automatischen Zuweisung von Aufgaben an Maschinen.
Wie funktioniert das System?
- Es überwacht die Abläufe im Werk
- Analysiert automatisch DXF-Dateien und erkennt die Form des Bauteils
- Prüft die Geometrie auf Korrektheit
- Generiert optimale Schnittparameter
- Weist die Aufgabe selbstständig der passenden Maschine zu – ganz ohne manuelles Eingreifen durch den Bediener
Zunächst erstellten wir ein MVP, das mit 500 Beispieldateien arbeitete. Langfristig soll das System bis zu 35.000 Varianten abdecken. Und das Wichtigste? Das System funktioniert mit der älteren Maschine – jener, bei der die Kosten pro Teil nur 0,5 Cent betragen – im Vergleich zu 1 Cent bei der modernen Ausrüstung.
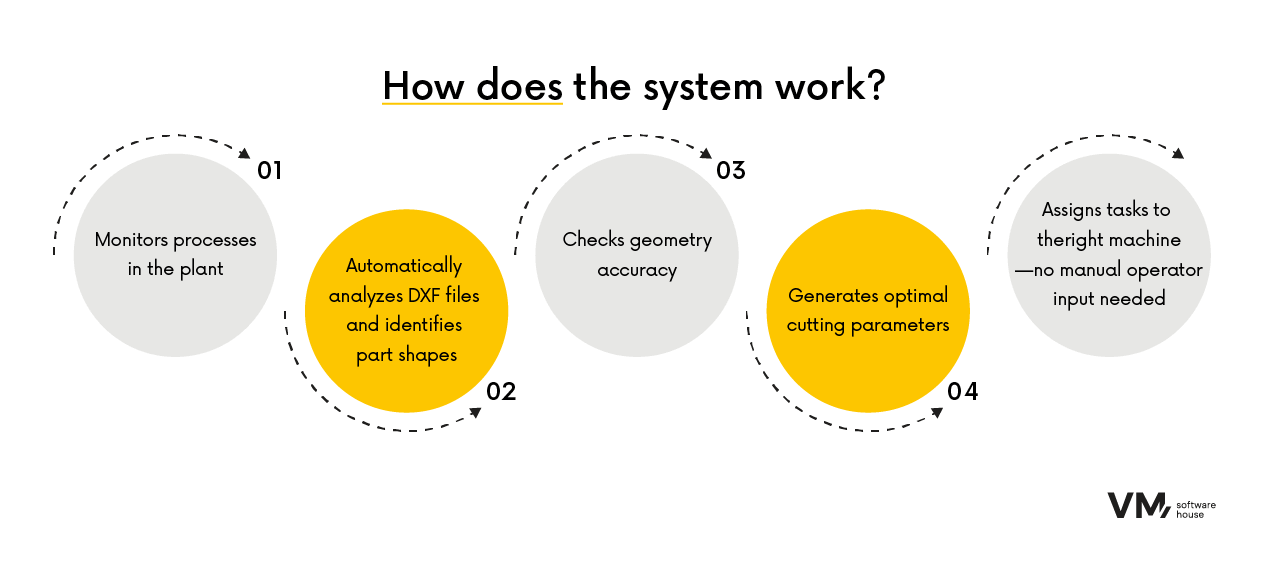
Ergebnisse
Dank der Automatisierung konnte ein großer Teil der Produktion auf die günstigere Maschine verlagert werden – ganz ohne Fehlergefahr und ohne ständige Anwesenheit erfahrener Bediener.
Der Produktionsprozess wurde:
- Deutlich schneller
- Weniger fehleranfällig und materialschonender
- Kosteneffizienter
- Umweltfreundlicher
- Leichter zu steuern
Durch die Optimierung der Maschinennutzung und eine bessere Ressourcenauslastung erzielte der Kunde messbare Vorteile:
- 25.000–65.000 USD Einsparung jährlich (Maschinenbetrieb, Wartung)
- 4.800–6.300 kWh weniger Energieverbrauch pro Jahr
- 1,9–2,5 Tonnen weniger CO₂-Emissionen pro Jahr
- Potenziell bis zu 325.000 USD Einsparung in 5 Jahren und eine CO₂-Reduktion von 10–12 Tonnen.
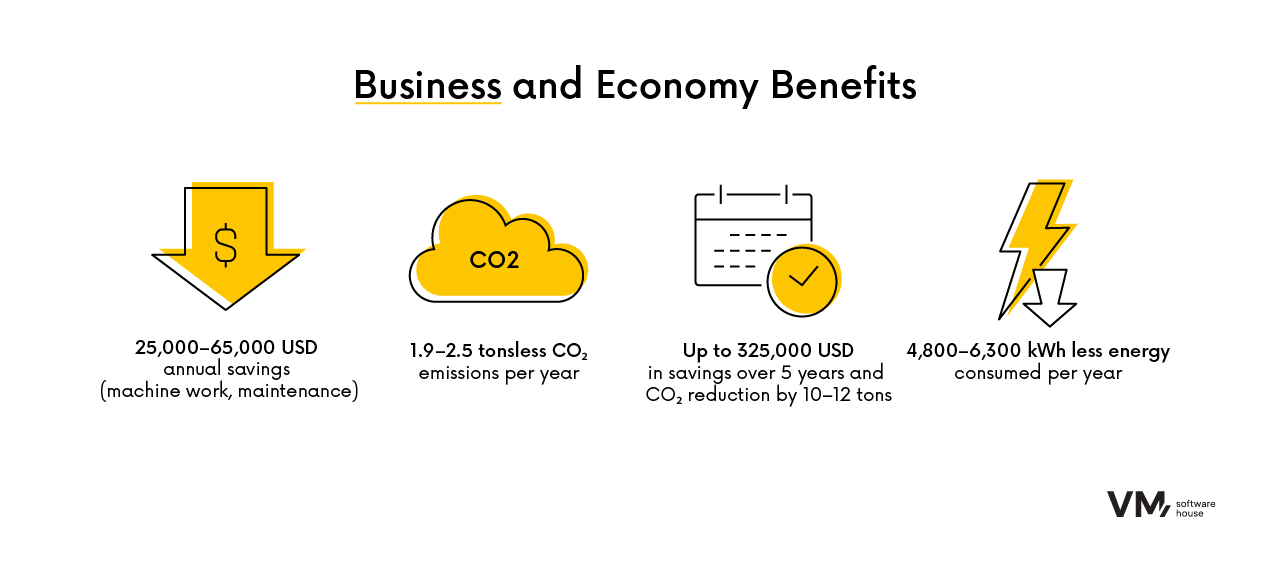
Kooperationsmodell
Daten- und Prozessanalyse
Wir haben den gesamten Prozess kartiert – vom DXF-Dateiimport bis zu den Maschineneinstellungen. Dabei untersuchten wir gezielt, wo Verluste entstehen und wie diese automatisiert vermieden werden können.
Startmodell mit großem Potenzial
Anfangs erkannte das Modell 500 Formen. Das genügte, um die Funktionsfähigkeit zu beweisen. In weiteren Phasen soll das System die gesamte Datenbank – bis zu 35.000 einzigartige Dateien – abdecken.
Integration ohne Hardwareaustausch
Das System wurde an die bestehende, ältere Maschine angepasst – ohne dass eine neue Maschinenflotte angeschafft werden musste.
Tests unter Produktionsbedingungen
Das System wurde direkt in der Produktionslinie getestet – mit realen Dateien und im tatsächlichen Arbeitsrhythmus des Werks.
Dokumentation und Weiterentwicklung
Der Kunde erhielt eine vollständige Dokumentation sowie die Möglichkeit, das Modell eigenständig weiter zu skalieren.
Technologien
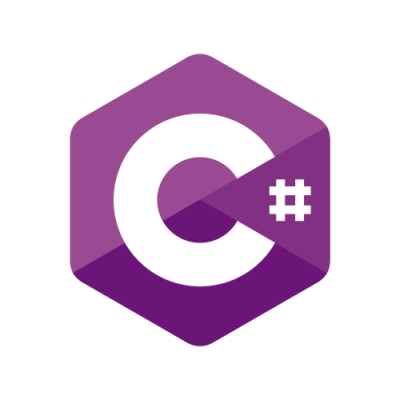
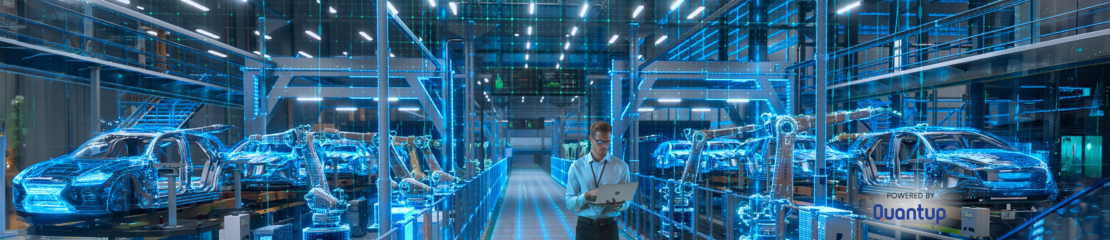
Helpdesk für die Fabrik – Intelligente Instandhaltungsunterstützung basierend auf KI und Werkshallenwissen
Design, Entwicklung, DevOps oder Cloud - welches Team brauchen Sie, um die Arbeit an Ihren Projekten zu beschleunigen?
Chatten Sie mit unseren Beratungspartnern, um herauszufinden, ob wir gut zusammenpassen.
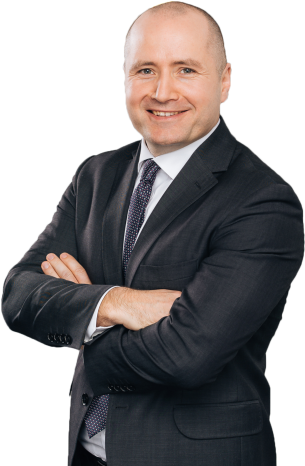