Diese Website verwendet Cookies, damit wir dir die bestmögliche Benutzererfahrung bieten können. Cookie-Informationen werden in deinem Browser gespeichert und führen Funktionen aus, wie das Wiedererkennen von dir, wenn du auf unsere Website zurückkehrst, und hilft unserem Team zu verstehen, welche Abschnitte der Website für dich am interessantesten und nützlichsten sind.
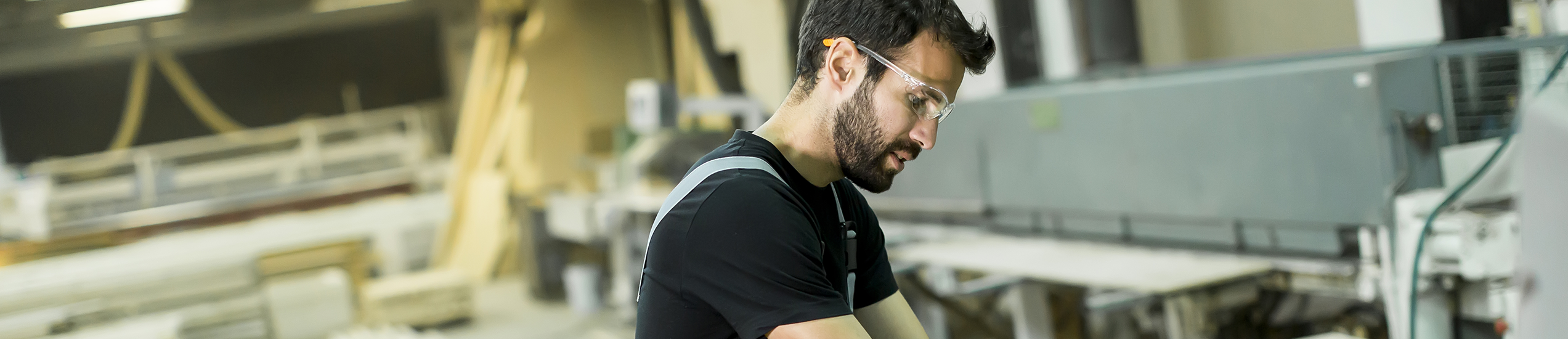
Kunde
Steinemann Technology AG ist ein weltweit führender Hersteller von Schleifmaschinen für Holzplatten und UV-Lackiersystemen für die grafische Industrie. Seit über einem Jahrhundert liefert das Unternehmen innovative Lösungen, die den Fortschritt in der Fertigungsindustrie vorantreiben. Angesichts wachsender betrieblicher und technologischer Anforderungen sah sich Steinemann gezwungen, sein bestehendes Maschinensteuerungssystem zu modernisieren, das den heutigen UX-Standards nicht mehr entsprach und die Produktionseffizienz einschränkte. Gesucht wurde eine Lösung, die nicht nur bestehende Einschränkungen beseitigt, sondern auch die Grundlage für eine zukünftige Digitalisierung und Prozessoptimierung schafft.
Herausforderung
Ziel des Projekts war die Entwicklung eines neuen Systems zur Automatisierung des Schleifprozesses. Die neue Lösung sollte die Produktionseffizienz verbessern, die Modularität erhöhen, die Wartungskosten senken und eine bessere Qualitätskontrolle unter Fabrikbedingungen ermöglichen.
Steinemann wandte sich mit der Bitte an uns, eine Vision für die Weiterentwicklung seiner Software zu erarbeiten und ein neues System gemäß Best Practices umfassend zu implementieren. Das Projekt wurde in enger Zusammenarbeit mit dem Kunden durchgeführt, was eine laufende Präzisierung der Anforderungen, eine schnelle Kommunikation über Risiken sowie die gemeinsame Entwicklung optimaler Lösungen ermöglichte.
Bei Steinemann bilden Präzision, Effizienz und reproduzierbare Ergebnisse die Grundlage der Tätigkeit. Das bisherige Qualitätsmanagementsystem für die Plattenproduktion stellte jedoch ein Hindernis für die Weiterentwicklung dar.
Die größten Probleme umfassten:
- Die Daten von Sensoren und Maschinen wurden synchron mit erheblichen Verzögerungen verarbeitet – Änderungen der Prozessparameter erschienen auf der Benutzeroberfläche mit bis zu 10 Sekunden Verzögerung. In der Praxis war es den Bedienern dadurch unmöglich, in Echtzeit Entscheidungen zu treffen – bis ein Problem erkannt wurde, konnte das Produkt bereits fehlerhaft bearbeitet sein.
- Fehlender Fernzugriff und Einschränkungen beim Monitoring – das Qualitätsmanagementsystem funktionierte nur lokal an den Maschinen, und die IT-Abteilung hatte keinen Zugriff auf die Arbeit der Geräte. Ohne zentralen Zugriff war die Fehlerdiagnose erschwert, und das Fehlen von Ereignisprotokollen verhinderte eine Problemanalyse.
- Komplexe Benutzeroberfläche – Bediener mussten lange Schulungen absolvieren, um das System effektiv zu nutzen, und die Bedienung erforderte viele manuelle Schritte.
- Schwierigkeiten bei Wartung und Weiterentwicklung des Systems – Änderungen und neue Funktionen einzuführen war zeitaufwendig und teuer. Selbst die Modifikation eines einzelnen Buttons konnte mehrere Monate dauern. Zudem erforderte der Mangel an Modularität Eingriffe in die gesamte Anwendung, und jedes Update brachte das Risiko neuer Fehler mit sich.
Steinemann benötigte eine moderne Lösung, die die operative Effizienz erhöht, den Arbeitskomfort der Bediener verbessert und eine einfache Erweiterung des Systems in der Zukunft ermöglicht.
Unsere Lösung
Um den Erwartungen des Kunden gerecht zu werden, schlugen wir vor, ein neues Qualitätsmanagementsystem für Platten von Grund auf zu entwickeln – mit moderner Architektur, hoher Datenverfügbarkeit und intuitiver Bedienung. Die wichtigsten Projektentscheidungen umfassten die Wahl einer modularen Architektur basierend auf Containern (Docker) sowie die Integration in die bestehende industrielle Infrastruktur des Kunden. Das neue System BQC Automation wurde als stabiles, zuverlässiges containerbasiertes System entwickelt, das sich einfach gleichzeitig auf mehreren Maschinen implementieren und aktualisieren lässt. Dank der Containerisierung können zukünftige Software-Updates reibungslos (praktisch ohne Ausfallzeiten) durchgeführt werden, was die Zeit für die Bereitstellung von Korrekturen und neuen Funktionen im Vergleich zum alten System erheblich verkürzt.
Systemarchitektur basierend auf OPC Connector
Der OPC Connector ist ein Vermittlungsmodul, das mit den Maschinen und Sensoren in der Halle kommuniziert. OPC sammelt in Echtzeit Prozessdaten (z. B. Walzgeschwindigkeiten, Stromverbrauch, Dicke der geschliffenen Platten), verarbeitet sie und sendet bei Bedarf Rückbefehle an die Steuergeräte. Dies ermöglicht eine geschlossene Steuerungsschleife – das System kann automatisch Maschinenparameter anpassen, um eine stabile Produktionsqualität aufrechtzuerhalten.
Wir entwickelten einen speziellen Algorithmus zur Qualitätskontrolle des Schleifprozesses, der basierend auf Sensordaten die Maschinenbelastung in Echtzeit reguliert, um eine Überlastung zu verhindern und eine gleichbleibende Qualität jeder Platte zu gewährleisten.
Dank der neuen Architektur sind alle Produktionsdaten sofort verfügbar – wir reduzierten die Verzögerung beim Lesen der Parameter auf <100 ms, was in der Praxis bedeutet, dass die Arbeit in Echtzeit erfolgt. Das vorherige System aktualisierte die Daten etwa alle 10 Sekunden. Diese deutliche Verbesserung der Reaktionsfähigkeit wurde unter anderem durch die Auslagerung eines dedizierten OPC-Connectors erreicht – einer separaten Kommunikationsschicht mit der Maschine, die den Datentransfer verbesserte (zuvor war die OPC-Bedienung „im Code“ der alten Anwendung eingebettet und ineffizient).
Neue Benutzeroberfläche
Großen Wert legten wir auf die neue Benutzeroberfläche. Unser Ziel war es, ein Qualitätsmanagementsystem für das Schleifen zu schaffen, das den Maschinenbedienern maximal entgegenkommt, die Produktivität steigert und die Fehlerhäufigkeit verringert.
In diesem Bereich führten wir gemeinsam mit dem Kunden eine UX-Analyse der bestehenden Lösung durch und trafen auf dieser Basis mehrere wichtige Designentscheidungen:
- Vereinfachung der Benutzeroberfläche – die neue Anwendung enthält nur notwendige Funktionen, und die Anordnung der Bildschirme wurde so umgestaltet, dass sie den Benutzer kognitiv entlastet und die Navigation erleichtert. Überflüssige Schritte und Informationen, die die Bediener im alten System ablenkten, wurden eliminiert.
- Intuitivität – wir setzten moderne UX/UI-Designmuster ein, wodurch die Systembedienung intuitiver und konsistenter mit den Erwartungen der Benutzer wurde, die an moderne Anwendungen gewöhnt sind. Steuerelemente sind logisch gruppiert, und Warnmeldungen sowie Hinweise werden verständlich formuliert. All das verkürzt die Schulungszeit für neue Bediener.
- Personalisierung und Flexibilität – die neue Software wurde modular aufgebaut, sodass Funktionen je nach Bedarf der jeweiligen Fabrik angepasst werden können. Bei Bedarf lassen sich Zusatzmodule (Add-ons) ohne Änderungen am Anwendungskern hinzufügen.
- Administratoren haben nun die Möglichkeit, Berechtigungen und Benutzeroberflächen für verschiedene Rollen (z. B. Bediener, Ingenieur, Manager) zu konfigurieren – so sieht jeder nur die für ihn relevanten Funktionen.
- Das System stellt außerdem eine webbasierte Oberfläche zur Verfügung, die über Browser (Chrome, Firefox, Edge) zugänglich ist. Sie kann auf jedem Computer oder Tablet im Firmennetzwerk gestartet werden, ohne dass eine spezielle Softwareinstallation auf jeder Maschine erforderlich ist. Die Oberfläche ist responsiv und für schwierige Produktionsbedingungen optimiert (z. B. gut lesbar auf großen Bildschirmen in der Halle).
Die neue Lösung ist auf den Betrieb im erweiterten Ökosystem vorbereitet
Das System kommuniziert nicht nur mit Maschinen über OPC, sondern auch mit externen Plattformen wie der Azure Cloud des Kunden. Produktionsdaten können in die Cloud gesendet werden, was Fernüberwachung, Infrastruktur-Skalierung und Datenanalyse zur weiteren Optimierung ermöglicht. Auch Sicherheits- und Zuverlässigkeitsmechanismen wurden berücksichtigt. Das System verfügt über einen lokalen Datenpuffer für den Fall eines Netzwerkausfalls. So wird selbst bei einem Internetausfall weder der Maschinenbetrieb noch die Datenerfassung unterbrochen.
Bewährte 4D-Methodik
Angesichts der Komplexität des Projekts und der geschäftlichen Ziele des Kunden entschieden wir uns für unsere bewährte 4D-Methodik (Discovery, Definition, Delivery, Direction), unterstützt durch agile Methoden und Design Thinking. Dieses Arbeitsmodell ermöglichte eine iterative Ergebnislieferung bei gleichzeitiger Qualitäts- und Risikokontrolle.
- In der Discovery-Phase konzentrierten wir uns auf ein umfassendes Verständnis der Benutzerbedürfnisse und der zu lösenden Probleme – unter anderem durch Workshops mit den Ingenieuren von Steinemann, Analyse des Schleifprozesses und Untersuchung des bestehenden Qualitätssicherungssystems.
- In der Definition-Phase verfeinerten wir die funktionalen und nicht-funktionalen Anforderungen, entwickelten UX-Konzepte und entwarfen die Zielarchitektur des Systems. Dank schnellem Prototyping konnten wir die wichtigsten Annahmen frühzeitig mit dem Kunden validieren und notwendige Korrekturen vor der Implementierung vornehmen.
- In der Delivery-Phase war eine der größten technischen Herausforderungen die Integration mit der Maschine über OPC. Die Entwicklung eines zuverlässigen Connectors erforderte eine enge Zusammenarbeit zwischen unseren Entwicklern und den Ingenieuren des Kunden. Letztlich gelang es uns, eine stabile, schnelle Verbindung herzustellen. Parallel dazu verfeinerten wir den Algorithmus zur automatischen Qualitätskontrolle, der unter Produktionsbedingungen validiert werden musste. Unser Team besuchte zweimal das Werk des Kunden und führte Tests direkt an den Produktionslinien durch. Die „Live“-Tests bestätigten, dass die entwickelte Lösung den Erwartungen entspricht und tatsächlich die Produktqualität verbessert. Die letzten zwei Projektwochen widmeten wir ausschließlich dem Systemtest – sowohl automatisiert als auch manuell, einschließlich Akzeptanztests mit zukünftigen Benutzern. Dadurch konnten wir kleinere Mängel vor der Produktivsetzung erkennen und beheben.
- Die Direction-Phase, also die Implementierung und Nachbetreuung: Nach Abschluss der Entwicklungsarbeiten schulten wir die Bediener und unterstützten die Inbetriebnahme des Systems an der ersten Produktionslinie. Das neue Qualitätssicherungssystem wurde parallel zum bestehenden System (im Pilotbetrieb) eingeführt, um einen sicheren Vergleich zu ermöglichen. Die Bediener bewerteten das neue Interface sehr positiv – es erwies sich als übersichtlich und einfach zu bedienen, was die Annahmen zur verkürzten Schulungszeit bestätigte. In den ersten Wochen nach der Einführung leistete unser Team laufenden Support, z. B. Fernüberwachung des Systems oder schnelle Reaktion auf Benutzeranfragen. Nach der Pilotphase entschied sich der Kunde für eine schrittweise Einführung des neuen Systems auf weiteren Maschinen und Produktionslinien. Abschließend übergaben wir Steinemann die vollständige Projektdokumentation sowie Empfehlungen zur weiteren Systementwicklung.
Ergebnisse
Die Einführung des neuen Systems verbesserte die tägliche Arbeit der Bediener und das gesamte Management des Produktionsprozesses.
Der Kunde erzielte eine deutliche Verbesserung der Effizienz und Qualität im Schleifprozess. Dank automatisierter Qualitätskontrolle passt die Maschine ihre Arbeitsparameter kontinuierlich an, was zu gleichmäßigeren Produkten und einer Reduktion von Ausschuss führte.
Bediener erhalten Echtzeiteinblicke in den Prozess. Schlüsseldaten und Kennzahlen sind sofort auf übersichtlichen Dashboards verfügbar. Das Problem der Datenverzögerung wurde beseitigt. Operative Entscheidungen können sofort getroffen werden, und das System generiert automatisch Warnungen bei Abweichungen.
Die neue Benutzeroberfläche ist benutzerfreundlich und intuitiv. Die Schulungszeit für neue Mitarbeiter wurde von mehreren Tagen auf wenige Stunden reduziert.
Dank des modularen Aufbaus und der flexiblen Rollenkonfiguration unterstützt das System die Zusammenarbeit zwischen Abteilungen besser. Bediener konzentrieren sich auf ihre Aufgaben, während Prozessingenieure oder Produktionsleiter Zugriff auf fortgeschrittene Analysen haben – ohne in die Arbeit der Bediener einzugreifen.
Die Vereinheitlichung der Umgebung für das Qualitätsmanagement beim Schleifen ersetzte viele verteilte Arbeitsstationen durch ein zentrales System. Anstelle mehrerer separater Bildschirme und Computer für jede Maschine reicht jetzt ein Standardterminal mit Webbrowser. Das führt zu geringeren Hardware- und Wartungskosten. Die Softwaremodernisierung verlängerte auch den Lebenszyklus der Maschinen – durch kontinuierliche Überwachung und automatische Belastungsanpassung sind sie weniger anfällig für aus falschen Einstellungen resultierende Ausfälle.
Die gesamte Investition schuf eine solide Grundlage für zukünftige Verbesserungen. Steinemann erhielt eine moderne Plattform, die in nächsten Phasen um neue Funktionen erweitert werden kann – wie z. B. fortschrittliche Produktionsdatenanalytik, prädiktive Wartung oder Integration mit anderen Fabriksystemen.
Technologien
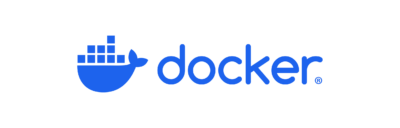
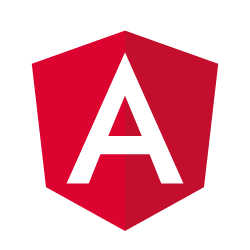
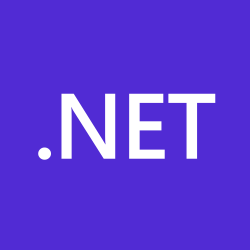
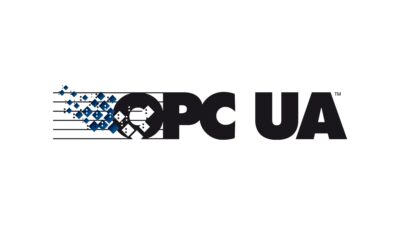
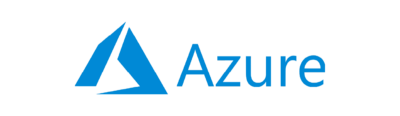
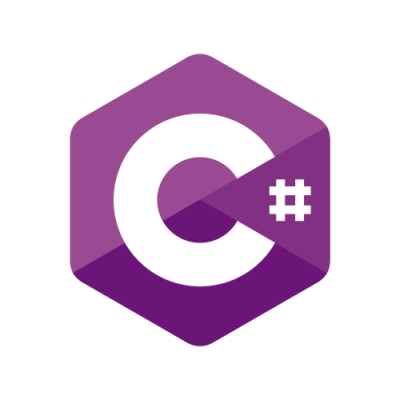
Kunde
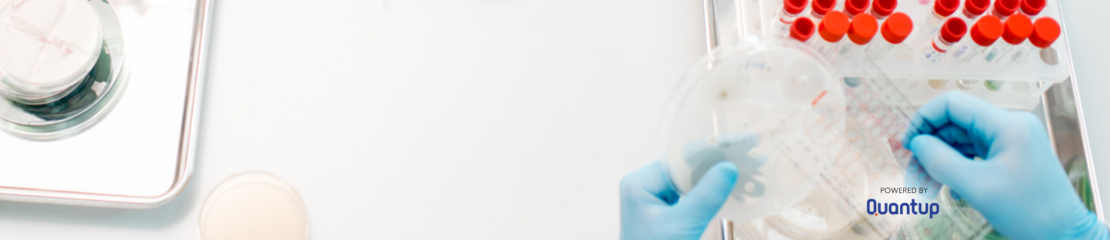
Design, Entwicklung, DevOps oder Cloud - welches Team brauchen Sie, um die Arbeit an Ihren Projekten zu beschleunigen?
Chatten Sie mit unseren Beratungspartnern, um herauszufinden, ob wir gut zusammenpassen.
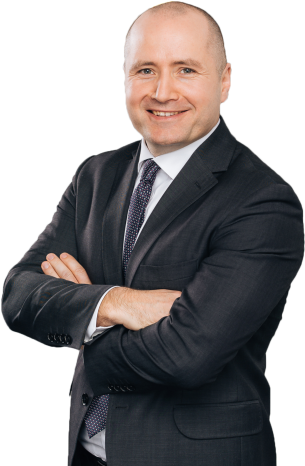