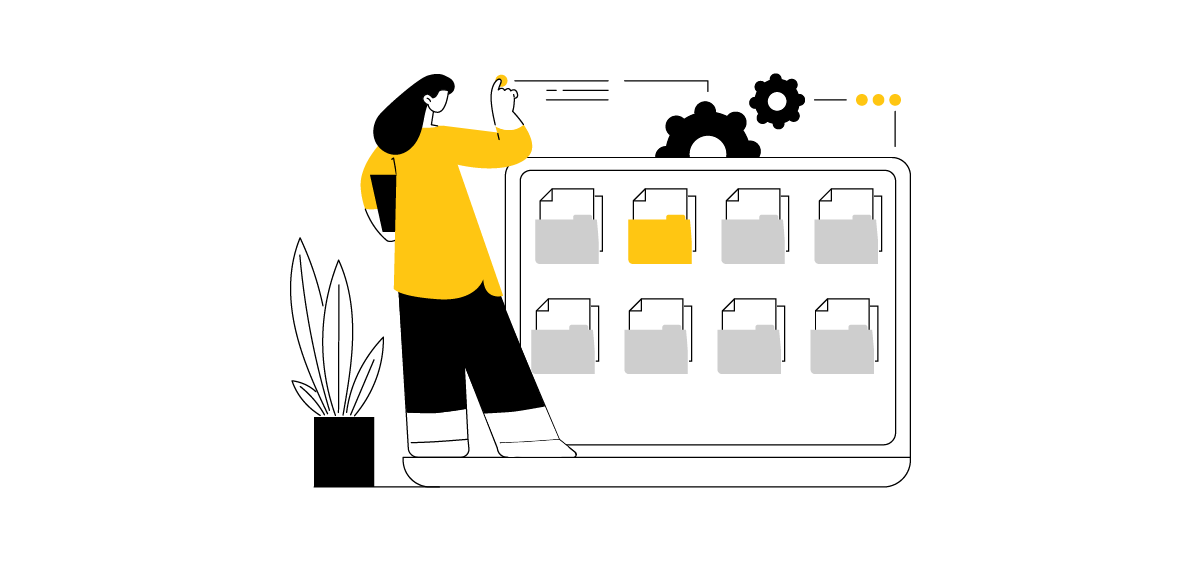
Die Fertigungsdatenverarbeitung birgt viele Herausforderungen. Dieser Artikel zeigt, wie das OPC-Gateway isolierte Datenspeicherung, alte Maschinenintegration und Echtzeitzugriff optimiert. Wir erläutern die Technologie, den Datenfluss vom Shopfloor in die Cloud sowie Anwendungsfälle in der Shopfloor-Digitalisierung. Zudem beleuchten wir die Rolle des OPC-Gateways in der Echtzeitanalyse, Prozessoptimierung und nachhaltigen Implementierung, mit einem Ausblick auf die Zukunft von OPC UA und Industrial IoT.
Inhaltsverzeichnis
Definition und Rolle: Was ist ein OPC Gateway und seine Bedeutung in der vernetzten Produktion?e
Das OPC-Gateway ist ein Tool, das auf der Basis des OPC UA-Protokolls arbeitet, einem der wichtigsten Kommunikationsstandards für die Industrie 4.0. Es handelt sich dabei um einen plattformunabhängigen Standard, der den sicheren und zuverlässigen Datenaustausch in der Industrie gewährleistet. Die Daten werden aus unterschiedlichen Quellen gesammelt und zentral ausgewertet. Bevor dieses jedoch geschehen kann werden unterschiedliche Kommunikationsprotokolle übersetzt, um die Daten einheitlich verarbeiten zu können. Einer der wesentlichen Vorteile dieses Systems ist die Echtzeitfähigkeit. Gemeint ist damit die Verarbeitung und Übertragung der Daten in Echtzeit. Dies ist ein großer Vorteil, weil damit die sogenannten Datensilos, die isolierte Datenspeicherung, aufgehoben wird.
In der folgenden Tabelle haben wir die wesentlichen Punkte des OPC-Gateways für Sie zusammengestellt und die Vorteile herausgearbeitet:
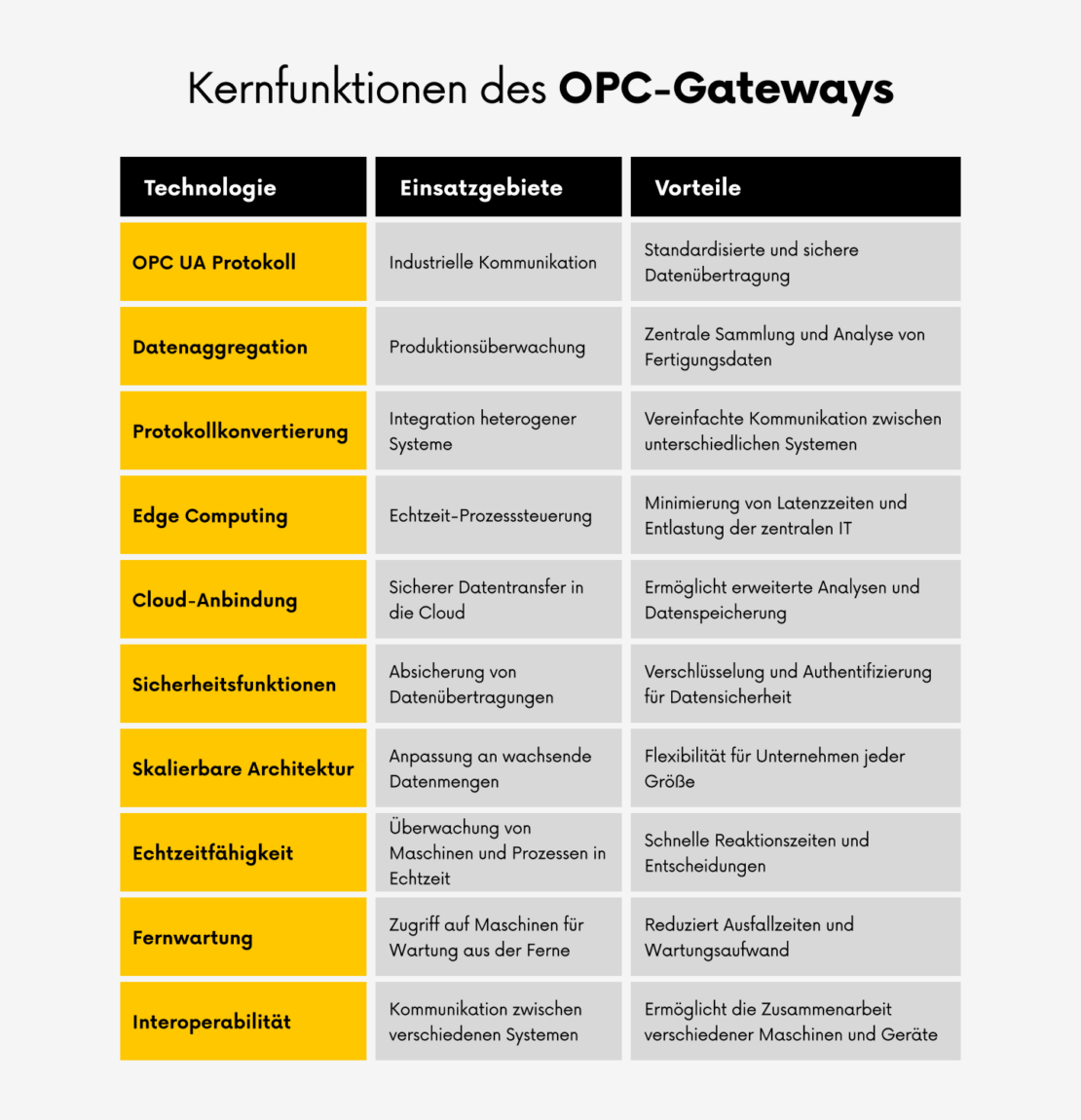
Datenfluss vom Shopfloor in die Cloud: Nahtlose Integration mit modernen Systemen
Das Gateway bindet Produktionsdaten effizient in übergeordnete Anwendungen ein, indem es sie in Echtzeit in die Cloud transportiert und dabei auch Altsysteme integriert. Für die Kommunikation werden standardisierte Protokolle wie OPC UA genutzt, die in der Lage sind, Maschinen und Systeme unterschiedlicher Hersteller zu integrieren. Die Produktionsdaten werden vereinheitlicht und über die Cloud-Services ausgewertet. Die Cloud hat den Vorteil, dass sämtliche Daten jederzeit und überall abgerufen und für alle denkbaren Analysen genutzt werden. Damit die Daten jederzeit verfügbar sind, sorgt das Gateway für eine automatische Synchronisation. Die so gewonnen Daten können ausgewertet und über Datenvisualisierung übersichtlich dargestellt werden.
All diese Daten werden zur Optimierung der Produktionsplanung wie Wartungsfenstern, Materialbeschaffung sowie Produktionsressourcen genutzt.
Herausforderungen der Datenintegration: Warum traditionelle Ansätze versagen
Alte Maschinen und fehlende Schnittstellen: Fabriken haben mit einer ganzen Reihe von Problemen zu kämpfen, wenn es um die Anbindung an moderne Technologien geht. Alten Maschinen fehlt beispielsweise oft die moderne Schnittstelle zur Datenübertragung. In diesen Fällen ist das OPC-Gateway in der Lage, eine Schnittstelle nachträglich zu erstellen und so den Datenfluss zu modernen Systemen zu gewährleisten. Im Vergleich zur Beschaffung neuer Maschinen mit den entsprechenden Schnittstellen entsteht für Unternehmen auf diese Weise ein großer wirtschaftlicher Vorteil.
Heterogene Systeme: Sie sind eine weitere Herausforderung für viele Unternehmen. Gemeint sind damit unterschiedliche Systeme, die in Unternehmen parallel laufen und nicht miteinander kommunizieren können. Auch hier kann das OPC Gateway Abhilfe schaffen. Es übersetzt die unterschiedlichen Systeme in eine einheitliche Sprache und ermöglicht so eine nahtlose Kommunikation der heterogenen Systeme und vereint sie so unter einem gemeinsamen Standard.
Fehlende Echtzeitdaten: Das OPC-Gateway ist in der Lage, Produktionsdaten, die bisher nur mit Verzögerung erfasst werden konnten, in Echtzeit zu übertragen. Dadurch können Entscheidungen wesentlich schneller getroffen werden.
Weitere Probleme, bei denen das OPC-Gateway hilfreich ist, sind beispielsweise eine unzureichende Datenqualität, dass das OPC-Gateway durch standardisierte Datenerfassung und -aggregation löst, oder komplexe Systemintegration und andere.
Best Practices für die Implementierung und den Betrieb von OPC UA Gateways
Das OPC-Gateway verfügt über diverse Möglichkeiten, datengetriebene Entscheidungen zu beschleunigen und Stillstände zu reduzieren.
Wir haben im Folgenden für Sie die 10 wichtigsten zusammengestellt:
- Prozessüberwachung
Das OPC-Gateway überwacht sämtliche Produktionsprozesse in Echtzeit und erkennt Ineffizienzen frühzeitig. - Predictive Maintenance
Durch die stetige Analyse von Maschinendaten werden Wartungsbedarfe rechtzeitig erkannt und Wartungstermine so gelegt, dass sie möglichst keinen negativen Einfluss auf den Produktionsprozess haben. - Optimierung des Produktionsdurchsatzes
Das OPC-Gateway kann auf der Basis der gesammelten Daten Engpässe erkennen und gegensteuern, sodass in der Folge die Produktionsleistung erhöht wird. - Fehlererkennung und Qualitätskontrolle
Sollte es zu Unregelmäßigkeiten im Produktionsprozess kommen, wird dies durch die Echtzeitüberwachung sofort erkannt, es wird gegengesteuert und die Produktqualität bleibt gewohnt hoch. - Datenbasierte Entscheidungen
Durch die Echtzeitüberwachung aller relevanten Systeme, können jederzeit fundierte und schnelle Entscheidungen getroffen werden. - Energieoptimierung
Die mithilfe des OPC-Gateways gewonnen Daten können ebenfalls zur Optimierung des Energieverbrauchs genutzt werden, um die Energiekosten zu senken. - Verbesserte Kommunikation
Durch die Integration aller Daten aus unterschiedlichen Quellen wird auch die Kommunikation zwischen den einzelnen Produktionsabteilungen verbessert. - Reduzierung von Stillständen
Die präventive Wartung der Maschinen führt nicht nur zu optimierten Produktionsverläufen, sie sorgt auch für eine Reduzierung der Stillstände. - Erhöhung der Flexibilität
Bei Marktveränderungen ist das System in der Lage, die Produktionsprozesse wesentlich schneller anpassen zu können - Erhöhung der Transparenz
Da alle Produktionsdaten jederzeit für alle Mitarbeiter sichtbar sind, wird für maximale Transparenz im gesamten Unternehmen gesorgt.
Sicherheit und Skalierbarkeit: Best Practices für nachhaltige OPC-Gateway-Implementierungen
Die Netzwerksicherheit sowie die Skalierbarkeit sind zentrale Themen in der modernen IT. Daher ist es wichtig, dass …
… für die Datenübertragung zwischen den Maschinen Verschlüsselungstechnologien wie TLS/SSL zum Einsatz kommen.
… über Zugriffsrechte nur autorisierte Personen an bestimmte Daten gelangen.
… für die Datenintegrität Prüfziffern und Hash-Algorithmen zur Sicherstellung der Daten während des Datentransports verwendet werden.
… redundante Systeme und Backups implementiert werden zur Verhinderung von Datenverlusten.
… die Cloud für die Skalierung der OPC-Gateway-Architektur genutzt wird, sodass das System bei wachsendem Datenvolumen problemlos erweitert werden kann.
Weitere wichtige Punkte in diesem Zusammenhang sind das Monitoring und die Alarmierung, automatisierte Software-Updates, eine Firewall-Integration, die Vermeidung von sogenannten Single-Points of Failure.
Ausblick auf die Zukunft: OPC UA, Industrial IoT und die nächste Generation von Fabriken
Alle Parameter weisen darauf hin, dass wir in den kommenden Jahren deutliche Verbesserungen der bestehenden sowie neue Technologien erwarten dürfen. Mit der 5G-Technologie wird die Echtzeitdatenübertragung noch schneller, die Künstliche Intelligenz wird ebenfalls stärker werden und Vorhersagen präziser treffen und Optimierungen vornehmen können. Dazu wird der Grad der Autonomie von Maschinen und Systemen zunehmen, wobei das OPC-Gateway als Kommunikationsbrücke dient. Auch im Bereich Industrial IoT (IoT) wird das OPC-Gateway eine noch zentralere Rolle spielen, indem es die reibungslose Kommunikation zwischen Maschinen und Systemen ermöglicht.
Es lohnt sich demnach, möglichst schnell in diesen Bereich einzusteigen, der sich so rasant entwickelt und heute wie auch in Zukunft den Standard in Sachen Optimierung Produktionsdurchsatz und Prozessoptimierung setzt, beziehungsweise setzen wird.
Genauere Einblicke zu diesem Thema finden Sie in unserem Case Study, in dem wir die Implementierung des OPC-Gateways bei einem unserer Kunden beschreiben. Dort erfahren Sie unter anderem, wie wir Daten auch von Sensoren erfassen, asynchrone Kommunikation einführen und den Software-Service remote durchführen können – ohne die Notwendigkeit, vor Ort zu sein oder sich per TeamViewer zu verbinden.